Long delivery times
Long delivery time due to border controls & food rerouting
Longer delivery times provide a risk to the quality of fresh products. And thus, a higher change of unnecessary food waste. Luckily, several Use Cases within IoF2020 work on products to improve chain transparency and mitigate this risk. With optimized packaging for example. And with sensors that provide detailed information during all the stages of transport. This information helps chain partners to take appropriate action in case of an event that affects the quality of the transported goods. No more disputes on responsibility or cause. Less food waste.
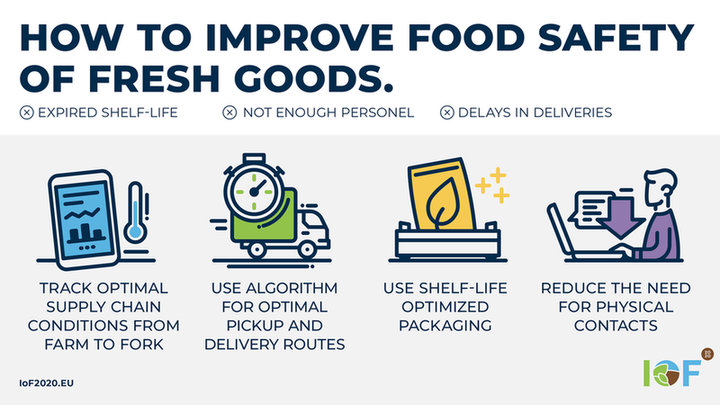
Smart food trays provide much needed insight in food chain
The fruit production chain faces different COVID-19 related challenges. As a result of closed borders and travel restrictions, seasonal workers can’t support harvesting activities. Longer delivery times, because many truck drivers fall into corona risk groups and werenot able to work. And changed consumer demand. When the lockdown started, people started to hoard products and the consumer demands for non-perishable products increased. However, the product developed within UC 3.4 Intelligent Fruit Logistics helps fruit producers, logistic partners and supermarkets to deal with these challenges.
Since June 2018, UC 3.4 installed over 200 smart food trays to monitor fresh food supply chains. This technology makes it possible to collect information on the supply chain (i.a. location, temperature and speed of the supply chain). For example, if trays are moving faster or slower than normal and where trays standstill or not. Valuable information when dealing with perishable goods, such as fruit.
''This technology shows what happens inside the fresh food supply chain.''
During the corona pandemic, the work of UC 3.4 has become even more important. By comparing data of involved partners from before and during the corona crisis deviations in the food production chain can be identified. For example, in retail differences in the speed of the supply chain where observed. In December (during Christmas) the average speed of the supply chain (from producer to distributer) was 10 days, in March (during the beginning of the lockdown) the average speed was 3 days and currently, the average speed is 7 days. This example shows the potential to make dynamic changes in the food production chain visible.
To use the full potential of UC 3.4, even more smart trays are needed. A joint approach is needed, to interpret the data together with different stakeholders. By working together, we can identify what is happening with our food supply chain, we can identify bottlenecks and we can think about solutions to overcome these challenges and improve efficiency, circularity and sustainability of the supply network. Now and after the corona pandemic!
- The IoF2020 COVID-19 Task Force about Use Case 3.4
Prolonging shelf-life: essential during the COVID-19 pandemic
Table grapes are economically important products in the Mediterranean region. Many factors contribute to the quality (e.g. colour, berry size and sugar rate “brix”) of the product. Table grapes are very vulnerable to pests, their shelf-life is limited and they are easily damaged during transport. Therefore, one could say that the production of high-quality table grapes is a challenge in general. As you can imagine, during the times of the COVID-19 pandemic, the production of high-quality grapes has become an even bigger challenge.
Let’s take a closer look at the work of the IoF2020 Use Case 3.1 Fresh Table Grapes Chain. Which corona-related challenges do they encounter, and which solutions do they provide? Use Case 3.1 developed an IoT network which makes it possible to monitor the whole table grape production chain, from field to fork. This IoT network has been used on different levels of the production chain and provides information on all the critical points in the process. These critical points include irrigation, table grapes managing, pest management and post-harvest. Over 40 sensors have been installed in 10 ha in Italy and 5 ha in Greece. By implementing this IoT network, the Use Case 3.1 aims to achieve better resource management (water, fuel and pesticide inputs) and higher fresh table grape quality.
''The production of high-quality table grapes is a challenge in itself, even more so with the challenges COVID-19 poses.''
The increased travel restrictions, stricter border controls and rerouting make it more difficult for transporters to deliver their products in the same amount of time. As a result of the increased delivery time, different challenges arise. A shorter shelf-life, and interrupted cool chain and potential shortages to name a few. All these challenges influence the quality of the fresh table grapes.
What does the Use Case 3.1 do to overcome these challenges and to guarantee the quality of the products? As a solution, shelf-life optimized packages (Blow ®) are used to increase the length of time that fresh table grapes can be stored. Consequently, the quality of the fresh table grapes is ensured, and the fresh table grapes remain fit for consumption, or sale. By using these kinds of creative solutions, IoF2020 use cases ensure that the food production chain remains of high-quality standard, from farm to fork. Even in these challenging times during the corona pandemic!
- The IoF2020 COVID-19 Task Force about Use Case 3.1
More transparency benefits stressed supply chains
COVID-19 puts food production chains under pressure in many different ways. From changes in demand to an increased risk of unforeseen delays along the way. ‘The stress on supply chains leads to an even bigger need for transparency between partners,’ says Mattia Nanetti, use case coordinator and co-founder of Wenda. Which is good, because that is exactly what Use Case 3.6 offers.
Shipment is the most critical part of the food-production chain for perishable and sensitive goods. The platform allows all partners to see how the products were conserved along the chain, from producer to point of sale. Humidity, temperature, location: visible to all partners. Real-time, if needed. Mattia: ‘If you know what has happened underway, and under who’s responsibility the goods were at the moment of say a sudden temperature rise, you can solve it immediately. There’s no dispute on who’s to blame. More clarity results in less dispute and a faster solution.’ The platform can cover not only the shipment phase but many more (i.e. inbound, storage, outbound).
''If you know what has happened underway, and under who’s responsibility the goods were at the moment of say a sudden temperature rise, you can solve it immediately.''
Mattia sees that many companies reconsider their strategy and are thus more open to start sharing data with chain partners. The increased demand for fresh and local goods in supermarkets also pushes suppliers towards more transparency.
With the experience gained in monitoring the handling of wine, the platform can be easily used in other chains where shipment is the critical factor. Are you interested in testing the platform in your logistic process? The basic features are set up in an hour, and UC 3.6 (Beverage Integrity Tracking) can advise you on what hardware suits your needs best too. ‘We are more than happy to share our findings with other partners,’ Mattia says.
- The IoF2020 COVID-19 Task Force about Use Case 3.6
IoF Taskforce
About Use Case 3.1, Use Case 3.4 and Use Case 3.6