Digital skills
Farmers’ unfamiliarity with digital tools
Even the best of digital tools is of no value when people don’t use it. The Use Cases within IoF2020 therefore do their utmost best to provide user friendly interfaces. They talk to farmers on a regular basis and test their minimum viable products on real farms in different countries. The feedback is used to make the products better and more user friendly. All with the aim to help more farmers make the transition and incorporate the use of digital tools in their daily business.
The Use Cases also organise demonstration events, so that the farmers participating in IoF2020 can share the benefits they experience with their colleagues. Due to the COVID-19 restrictions, these demonstration events now take an online form.
Next to that, IoF2020 use cases are working closely with test farms and farmers to understand their needs and develop products that are intuitive, with an enhanced user experience. The products and solutions themselves get enriched with the feedbacks from the farmers, and the farmers benefit from products that are easy to handle and truly supporting them in their farming operations.
As you can read in this newsletter, many of the IoF2020 Use Cases provide solutions to the challenges COVID-19 poses. As a result, COVID-19 pushes the use of sensors and data-analysis in the agri-sector.
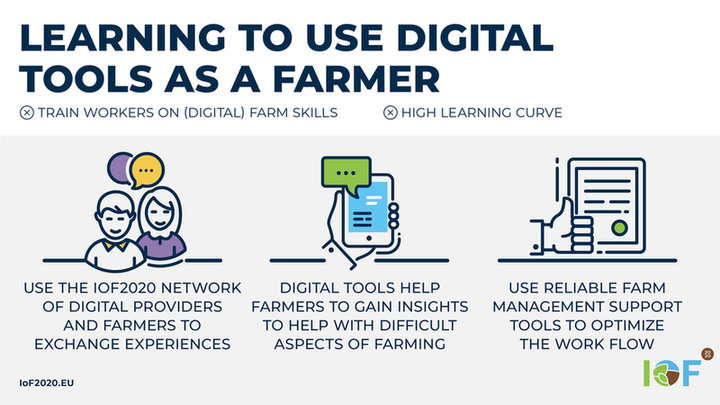
Feed supply chain management during the pandemic
The meat production sector is facing numerous challenges related to animal welfare: for instance, foreign competition, climate impact and antibiotic resistance. To overcome these challenges the IoF2020 Meat Trial implemented different IoT technologies, like early warning systems, advanced monitoring systems and tracking data apps. Our IoF2020 Use Case 5.5 Feed Supply Chain Management focuses on the animal feed industry. An IoT integral feedstock management system was implemented to make the whole supply chain more efficient. However, during the corona pandemic, additional barriers arose which challenged the work of UC 5.5.
The usual work of UC 5.5 consists of optimising the supply chain management. Different stakeholders like feed suppliers or livestock farmers struggle with the time and quality evaluation when restocking their feed silos. This significantly increases the cost and lowers labor efficiency. UC 5.5 implemented INSYLO technology to improve supply chain management. This technology consists of a 3D sensor which makes use of algorithms to collect important silo stock level information. This enables UC 5.5 to optimise refill orders, production batches, shipping routes and raw materials purchases.
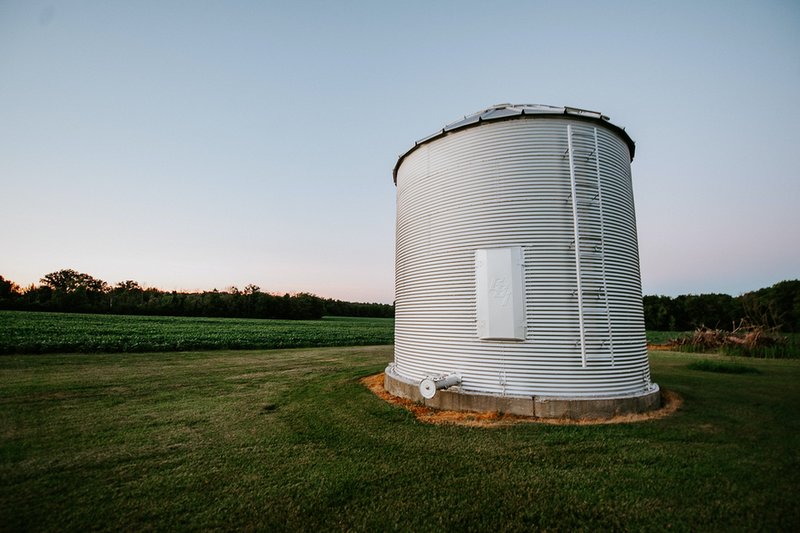
To overcome this challenge, UC 5.5 uses different digital tools. Supply and demand indicators are used to predict supply needs. Additionally, open-source algorithms are used to optimise pickup and delivery routes. Last, different tools are used to track and manage food supply remotely at different stages in the supply chain. These solutions help to overcome the barriers of these challenging times and helps to improve the efficiency of the feed supply chain.
Interestingly, UC 5.5 developed this logistic tool, the road planner. As explained, it is used for optimizing the delivery of feed. But they offered it spontaneously to hospitals and care centers in the Barcelona area. The hospitals now use the road planner to optimize their pickup of protective clothing (e.g. aprons and masks). This is a great example of how IoT can be shared and used in a wide community. The technology is also applicable cross-sectoral, and our use cases are willing to help.
- The IoF2020 COVID-19 Task Force about Use Case 5.5
IoF Taskforce
About Use Case 5.5