Article
What’s in the silo?
A Business Case in Development
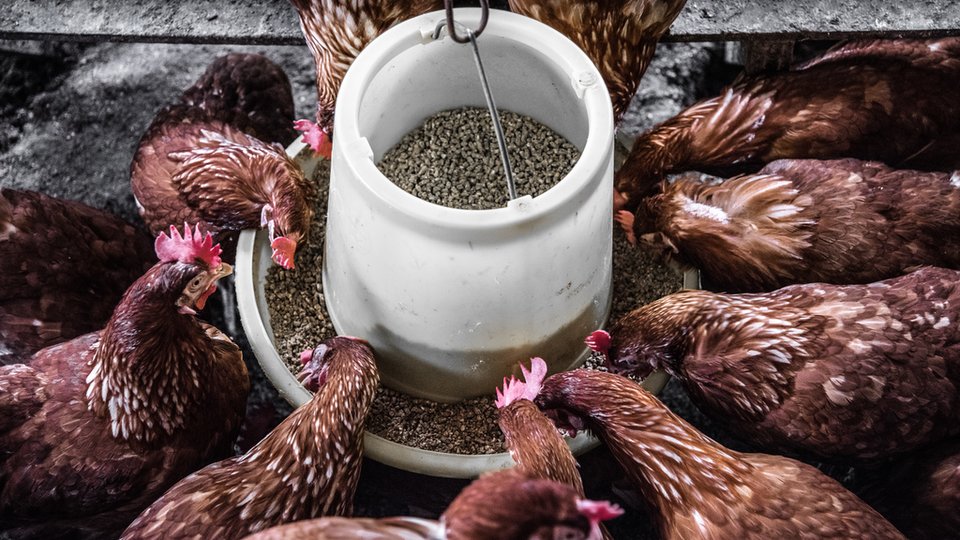
Feed silos are an integral part of the meat industry. Yet, many farmers and feed suppliers alike still struggle to streamline their feed silo restocking processes. Quantity evaluation can help improve timing, cut cost and decrease labor for both farmer and feed supplier. The ‘Feed Supply Chain Management’ use case (UC5.5) set out to develop an integral feedstock management system to optimize the entire supply chain. Through IoF2020 they have improved their innovative product ánd found opportunities for the further development of their business cases.
obody benefits from empty feed silos. Farmers who miscalculate the volume of feed left in their feed silo’s will need to place urgent orders. These orders are costly, both in terms of time and in terms of money. Not to mention the stress that comes with not being sure if your feed supply is going to last long enough for your order to arrive. On the other hand, unpredictable orders mean a less streamlined and less automated process for feed suppliers as well. Thus, both farmers and feed suppliers benefit from the optimization of the feed silo restocking process.
Feed silo monitoring: a task with many hurdles
Manual inspection of feed silo levels is labor intensive and sensitive to errors. Because of this, many feed level management solutions exist. However, getting consistent truly accurate measurements is difficult. Some sensors don’t take uneven surfaces of silo content into account in their calculations. Others rely on often unreliable internet connections or have high installation costs. And then we haven’t even mentioned the dependency on the electrical grid yet. In short: the road to the production of a truly reliable feed silo monitoring system is one with many hurdles.
The Feed Supply Chain Management use case set out to take these hurdles. Through IoF2020 use case partner INSYLO has been able to improve their monitoring system in a real life setting. Their monitoring system is based on using 3D cameras inside the silo that measures surface levels of silo content, calculate remaining feed volume, and offer accurate output in a user-friendly application. The sensors have integrated solar panels so that they are not dependent on a power grid, and by using a wireless sensor network they can even be used in areas without mobile coverage.
”The road to the production of a truly reliable feed silo monitoring system is one with many hurdles.”
However, all smart and high-tech solutions aside, these sensors were not yet as flawless as they seemed to be in a pre-commercial stage, and needed to be fully validated in different environments facing the most demanding conditions in real life outdoors before their market launch. IoF2020 offered the ideal testbed: real life test sites in different conditions throughout Europe, and real life user feedback from testing. The insights that real life testing offered has helped improve the product, and a new and sturdier version of the sensor has just been released.
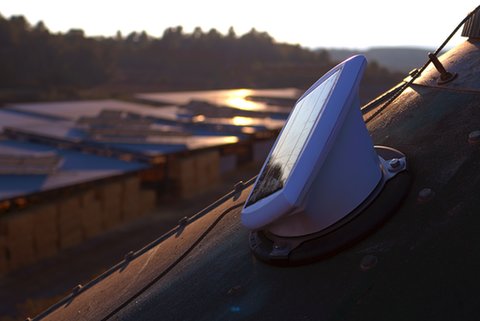
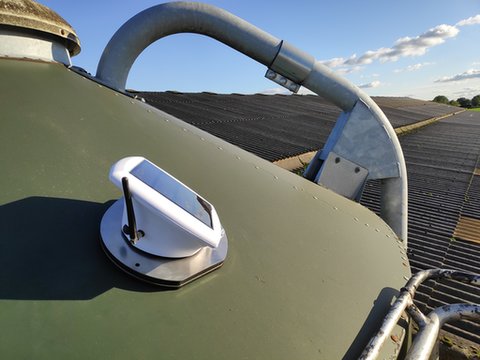
The feed silo sensor is a fully off-grid device, using solar power and a wireless network that is not dependent of mobile coverage.
A business case in development
When UC5.5 started out, one of the intended business case of the finished product was centered around offering sensors to farmers and asking a small fee for the data service. The interest from European farmers is clearly there: whilst the product is still in its test phase, the sensors have already been deployed in Spain, the UK, Sweden and Norway. However, the user feedback from farmers, interest from feed suppliers and the business development support team from IoF2020 have also confirmed the added value of further integration of the use case’s solution in the feed supply chain.
As already pointed out in the beginning of this article, nobody benefits from empty silos. The idea of selling sensors to farmers makes sense from the farmers’ perspective: a good monitoring system is of value to farmers because it saves them time, effort, and lowers the risk of running out of feed. However, further value can be added by also integrating the feed supplier in the supply chain. By offering data from feed silos directly to feed suppliers, farmers can help feed suppliers better predict the needs of their clients. Farmers and feed suppliers can even agree upon the automated re-supplying of silos as soon as volumes drop under a certain level.
”There are around 5 million feed silo’s in the world. 20% of these silo’s, 1 million in total, are handled by only 40 big feed suppliers.’’
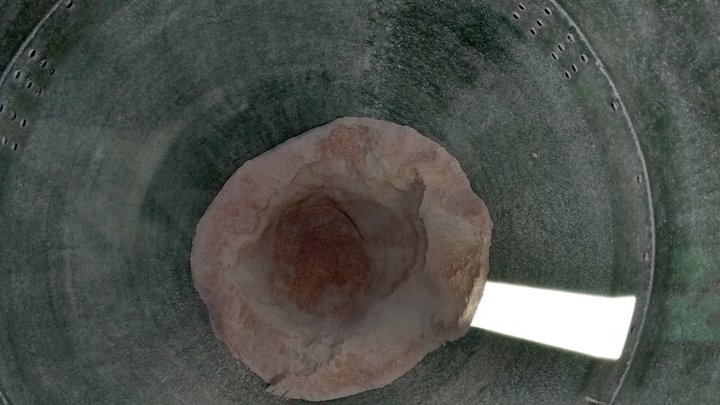
The inside of a feed silo. This image clearly shows one of the many factors that make accurate measurement of feed silo content difficult: silo content can be very unevenly distributed. By making use of 3D cameras the use case partners are able to conduct accurate and reliable measurements, with a maximum error below 3%.
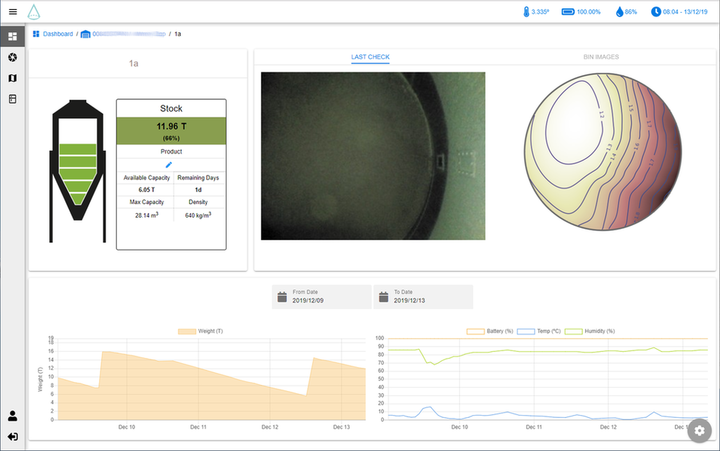
Through a user-friendly application farmers get information about the contents of their feed silos. Next to measuring the remaining stock, the sensor also measures other in-silo conditions such as temperature and humidity to help assess feed quality status.
By shifting the attention towards the added value of a good monitoring sensor for feed suppliers, a second business case is going to be explored. The idea is that feed suppliers can offer farmers sensors for free, or for a small fee, in exchange for the use of the data produced (and owned) by the farmers. This data (thanks to a Smart Logistics Platform that uses Artificial Intelligence algorithms) can help feed suppliers benefit from reduced urgent orders, improved batch production cycles, optimized delivery routes ,and even a lower exposition to raw materials market variances. The Feed Supply Chain Management use case now sets out to explore this second business model. For this, they aim to deploy another 175 devices in Spain before the end of 2020.
Next to adding an extra business model, focusing on feed suppliers has an added benefit. There are around 5 million feed silos in the world. 20% of these silo’s, 1 million in total, are handled by only 40 big feed suppliers. Focusing on these suppliers instead of on individual farmers offers the potential to scale up quickly and efficiently. If the use case partners are able to strike deals with one or more major feed suppliers, the effect will be enormous: many farmers will be able to benefit from the sensors, and the positive environmental impact of their solution will be more than substantial.
The unique value of IoF2020 for business development
Through IoF2020 the use case partners have been able to improve both their product and their business case. As Xavier Xirgu, Chief Innovation Officer from INSYLO, the producer of the sensors, puts it: ‘’IoF2020 has been a true supporter of our project, investing their time and efforts in our work beyond the normal scope of a European collaborative project.’’ He is especially pleased with the amount of progress made in the past year: ‘’the use case has put into test our devices and systems, forcing us to move forward and improve it. Furthermore, it has helped us further strengthen the business case for our product. We are truly grateful for this’’.